High-Quality Tactile Membrane Switch Just in One Place - The Ultimate Solutions
Your One-Stop Solution for Industrial and Consumer Applications
Hi, I’m Lily from SwitchNova. Let me introduce our Tactile Membrane Switch solutions.
We have over 10 years of experience in providing high-quality tactile membrane switches to global industry leaders. Explore our reliable and customizable solutions designed for industrial automation, medical devices, and consumer electronics.
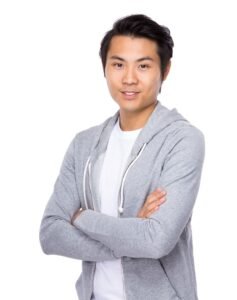
Why Choose SwitchNova ’s Switches
Reliable, high-quality switches designed for demanding applications and long-term performance.
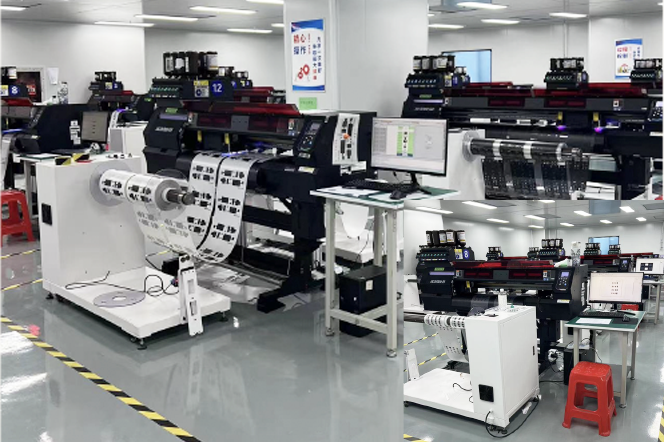
Advanced Manufacturing
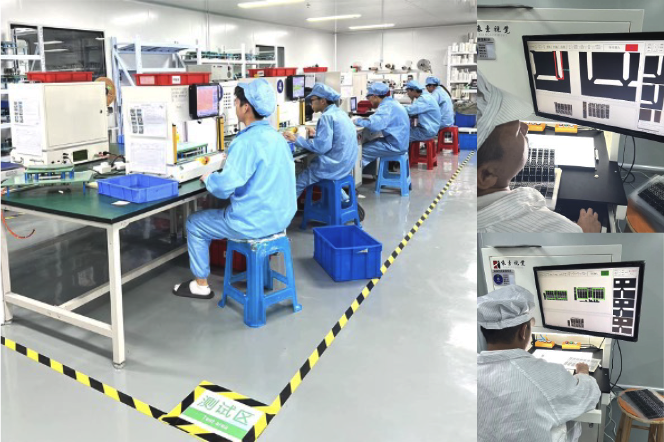
Strict Quality Control
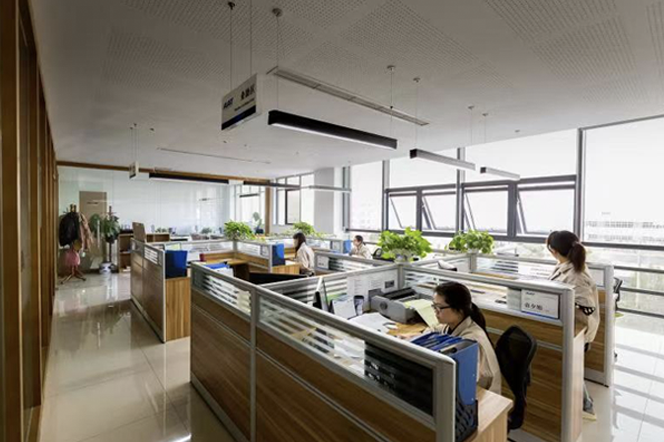
Fast and Efficient Response
Trusted by Global Brands
We proudly serve industry leaders with reliable, high-performance membrane switch solutions.
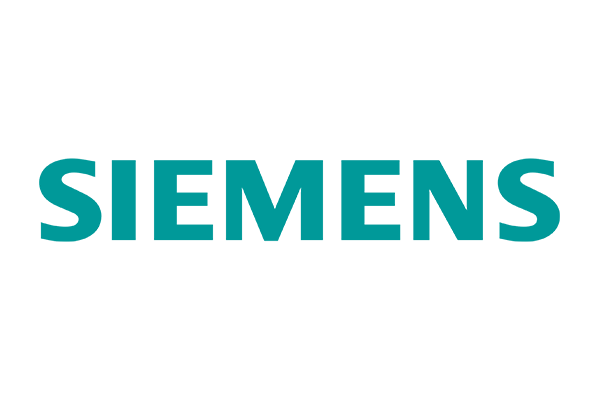
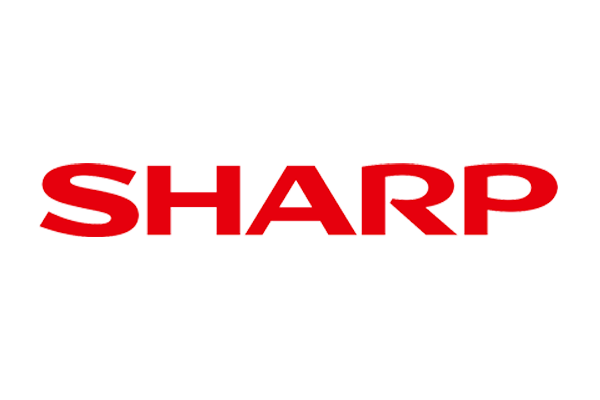
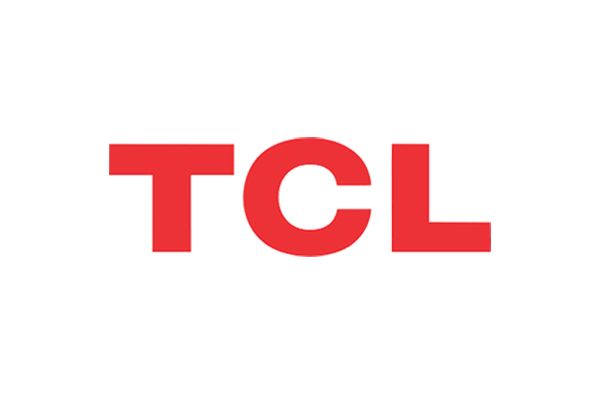
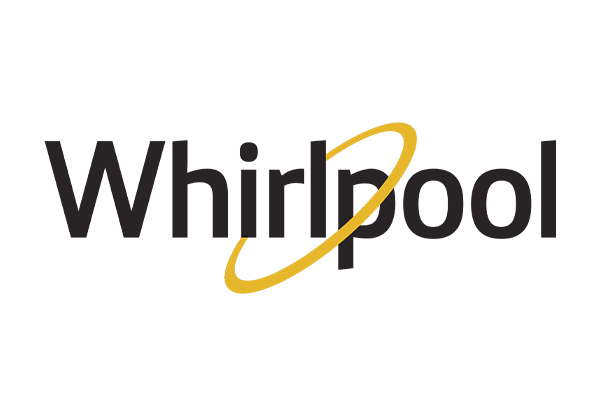
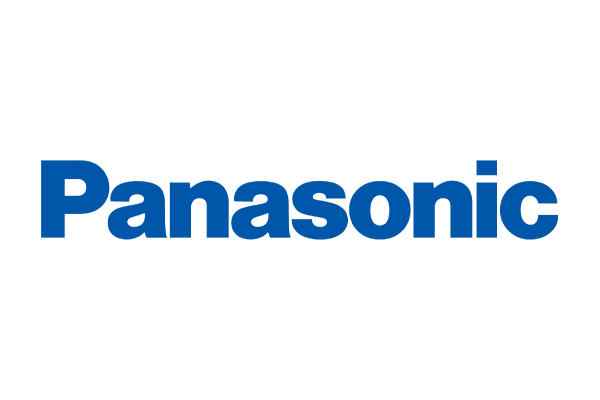
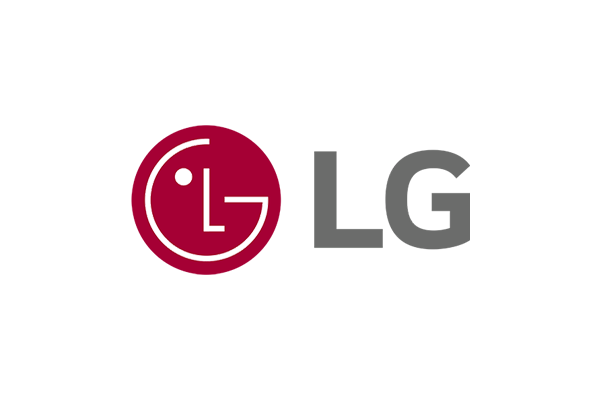
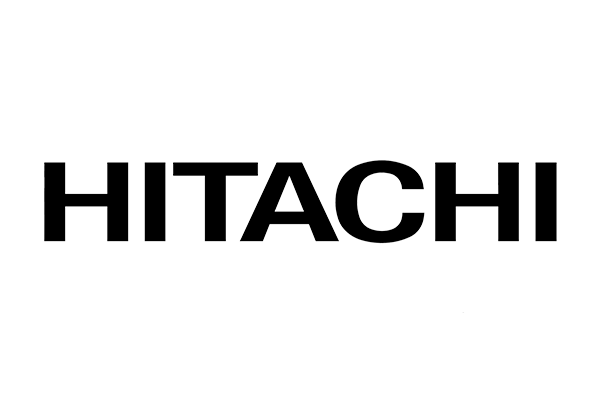
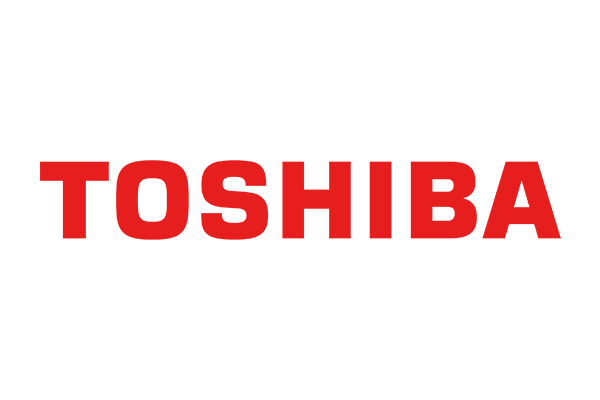
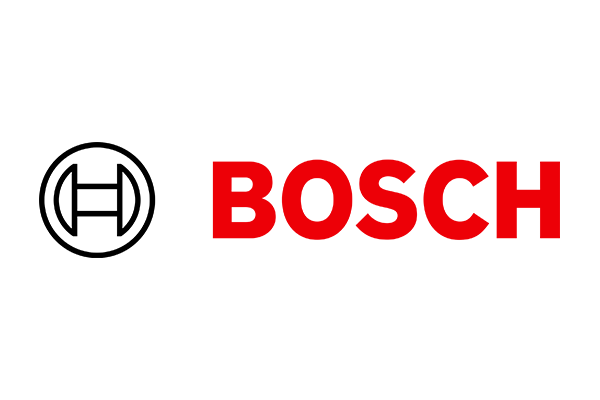
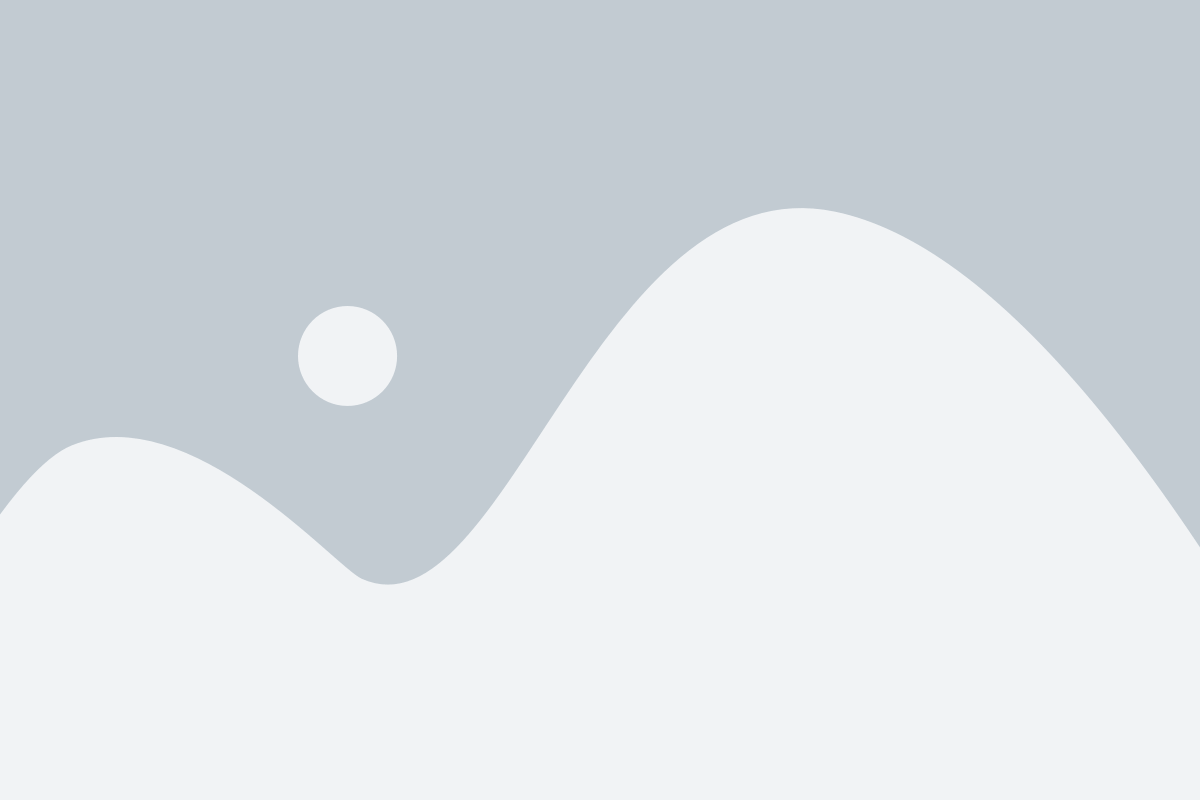
Our Best-Selling Tactile Membrane Switch
Discover our best-selling tactile membrane switches designed for various industries.
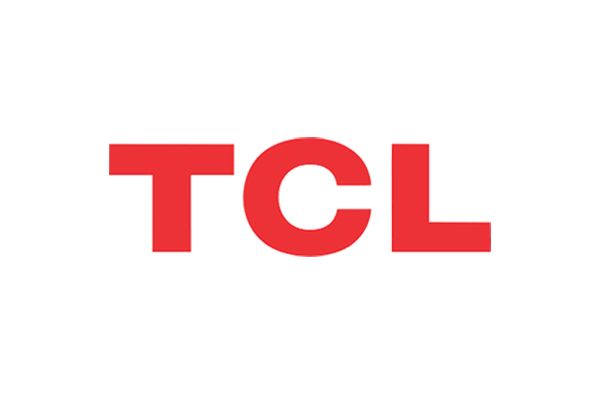
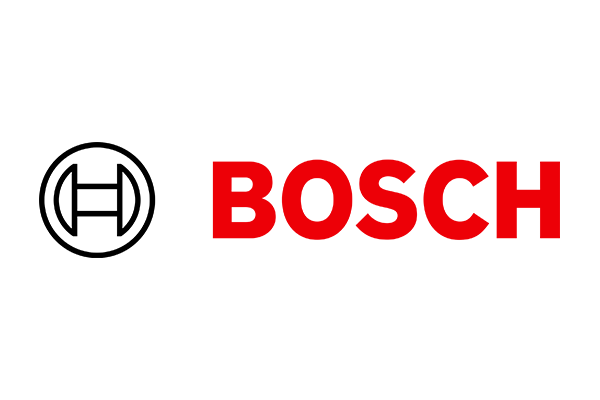
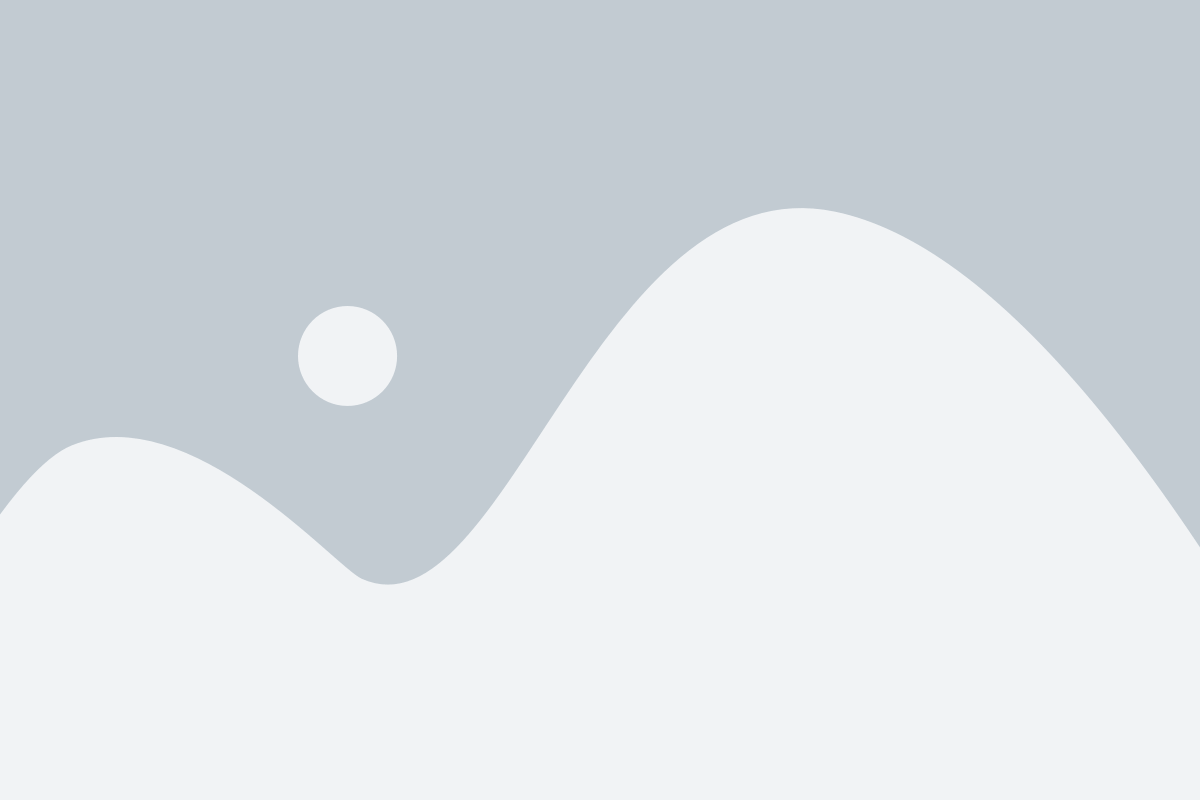
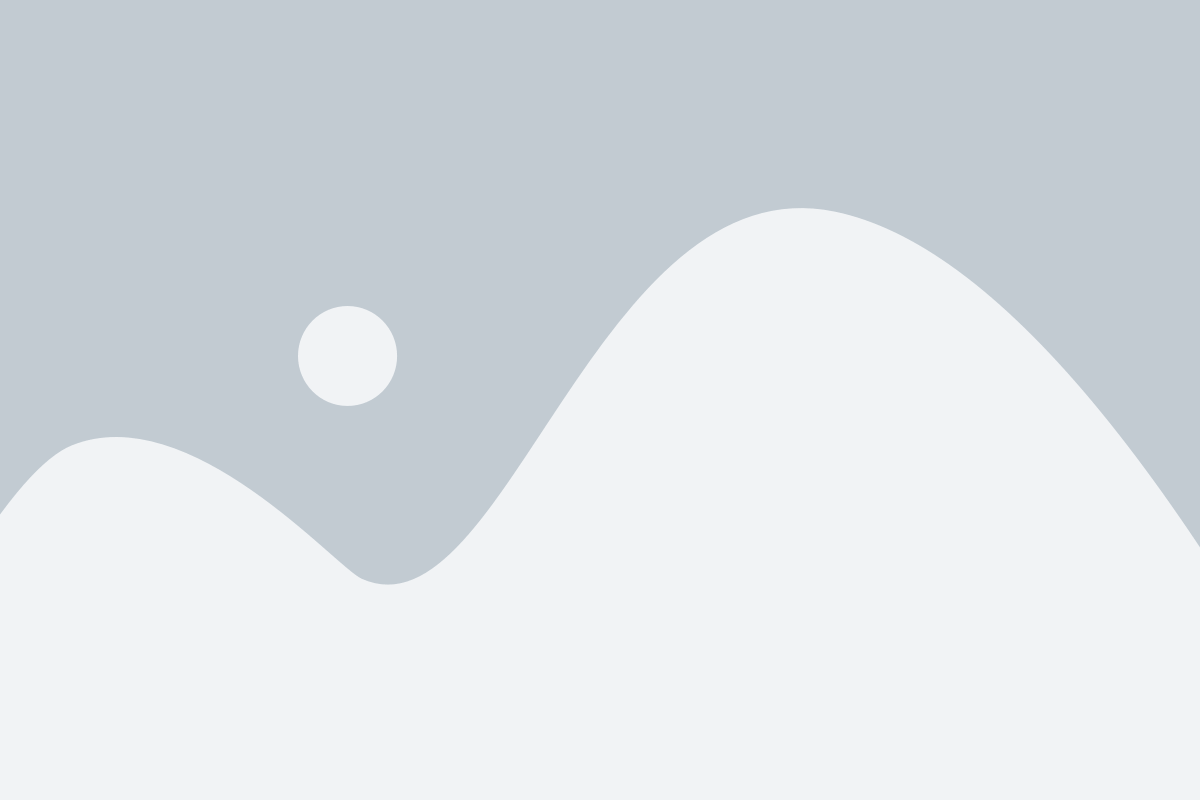
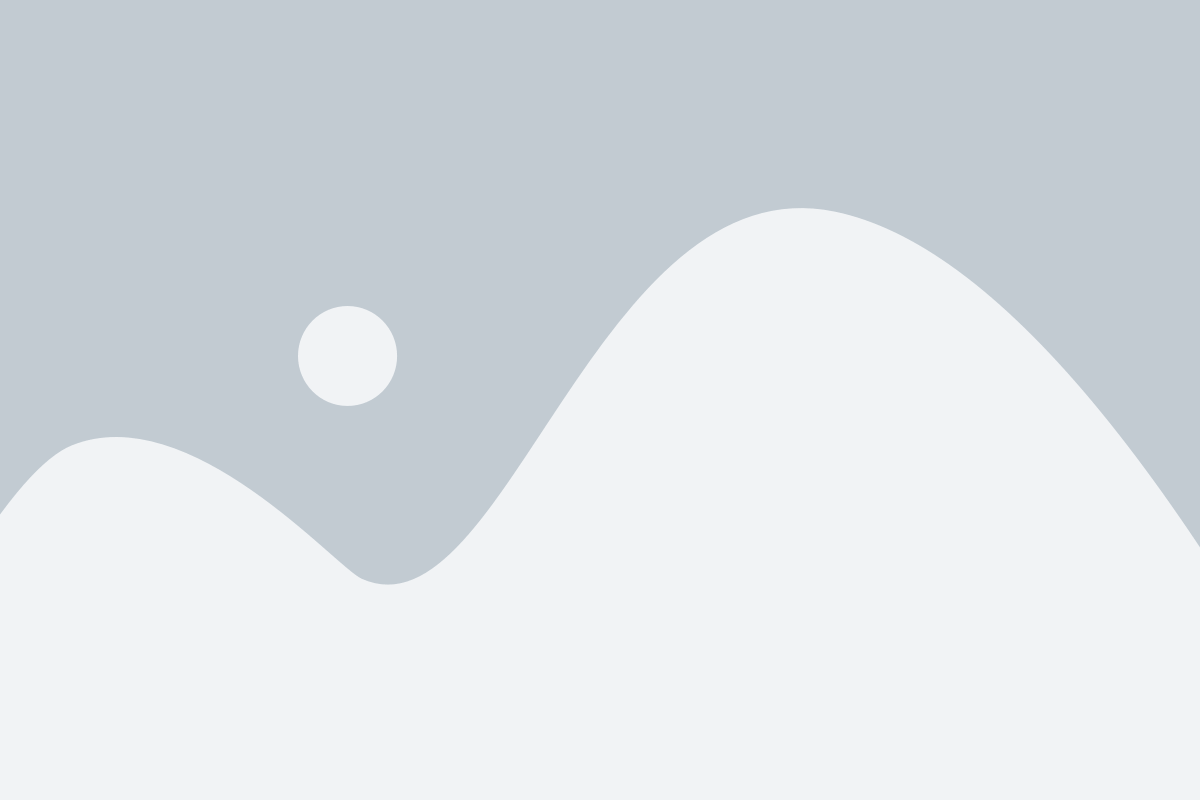
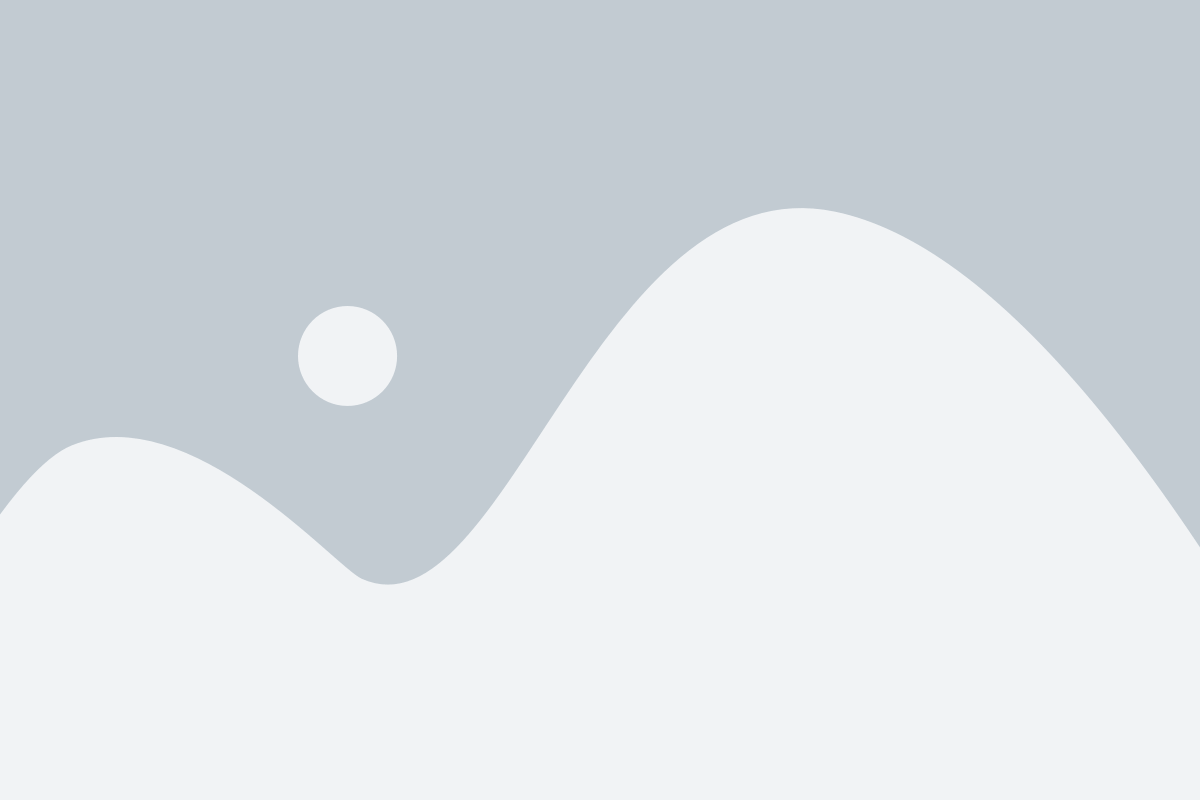
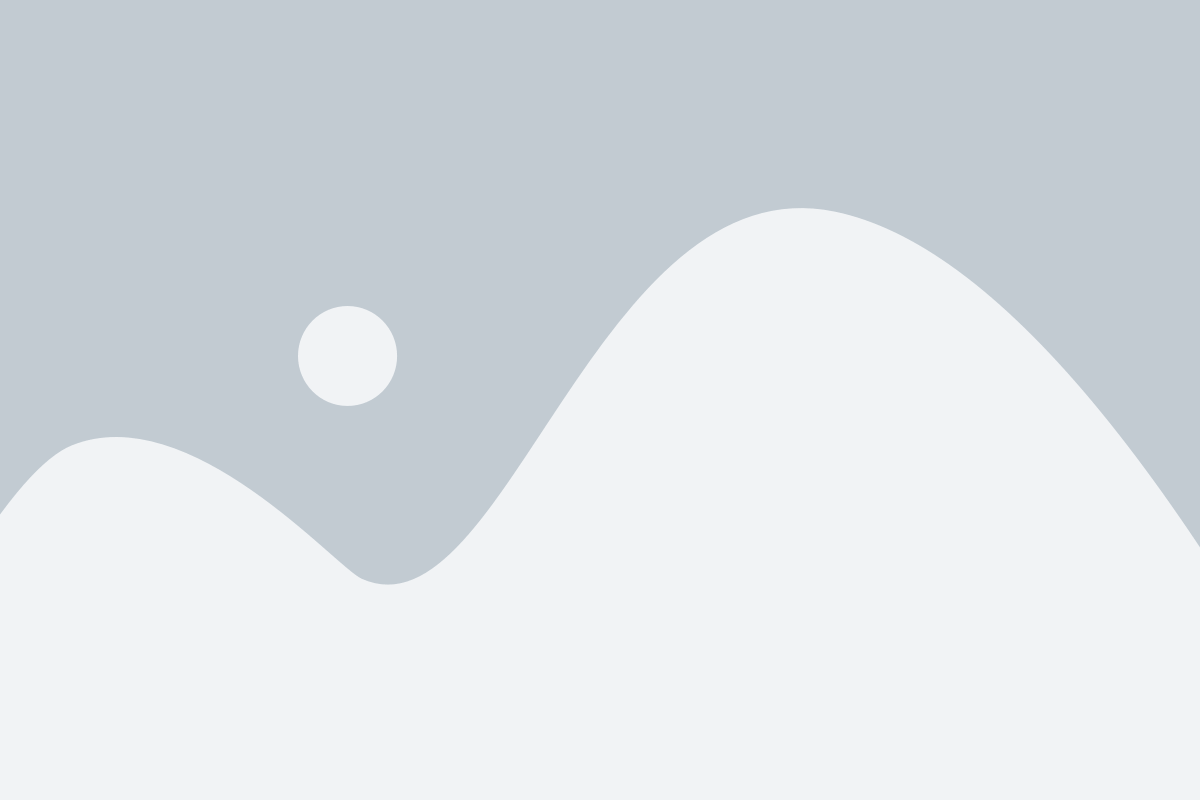
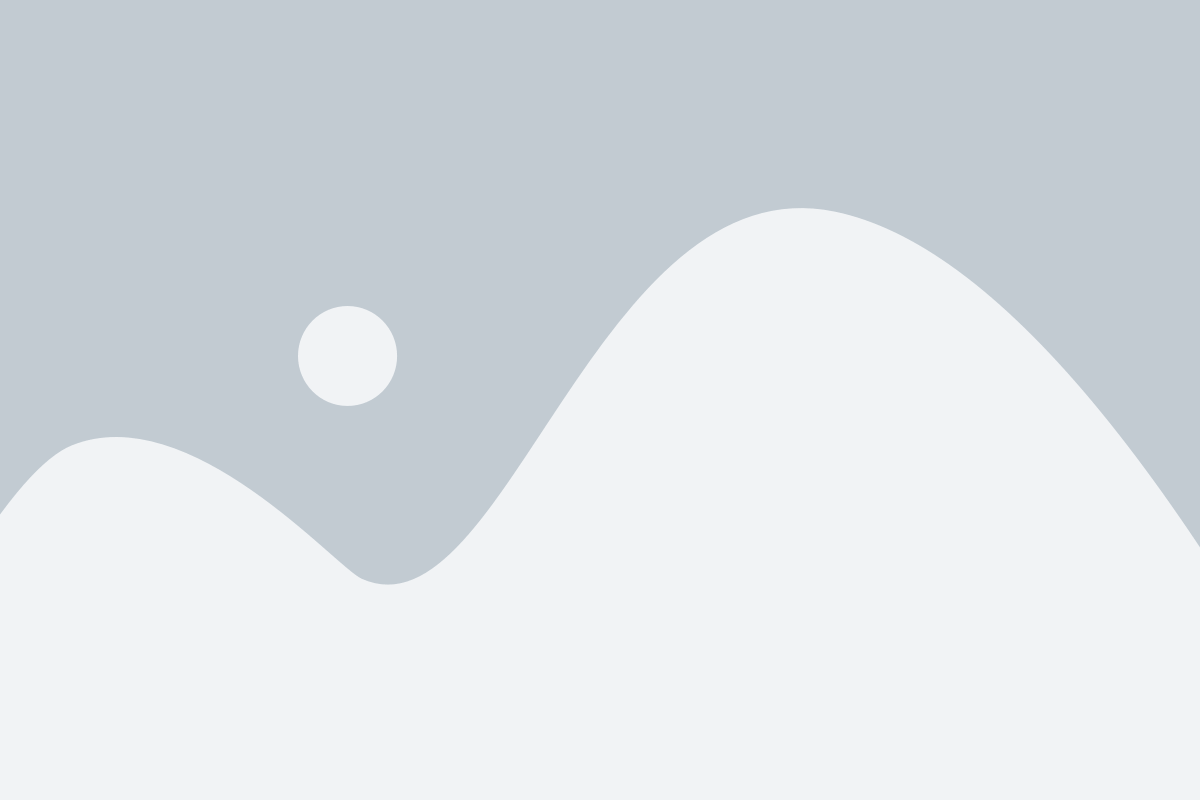
Our Best-Selling Tactile Membrane Switch
Discover our best-selling tactile membrane switches designed for various industries.
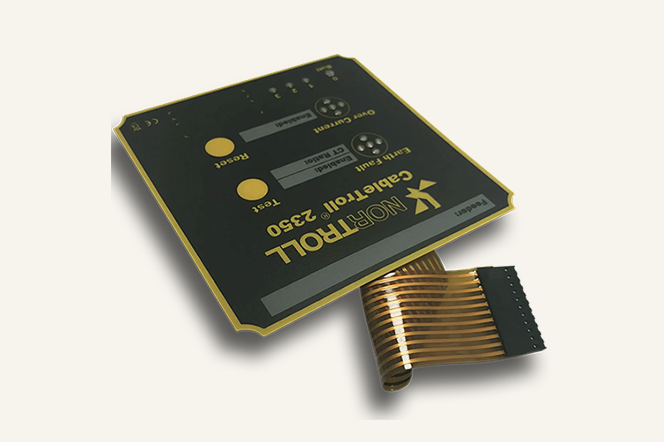
Tactile Membrane Switch
High tactile feedback, durable design for industrial and medical applications, IP65 rated.
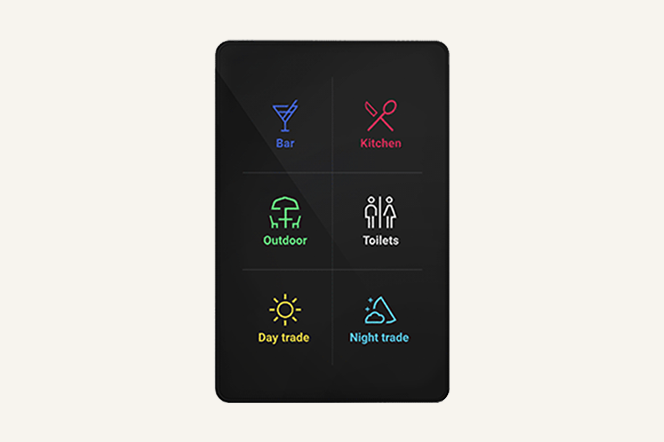
Capacitive Membrane Switch
Responsive touch control, anti-interference design for electronics and automotive, 10ms response.
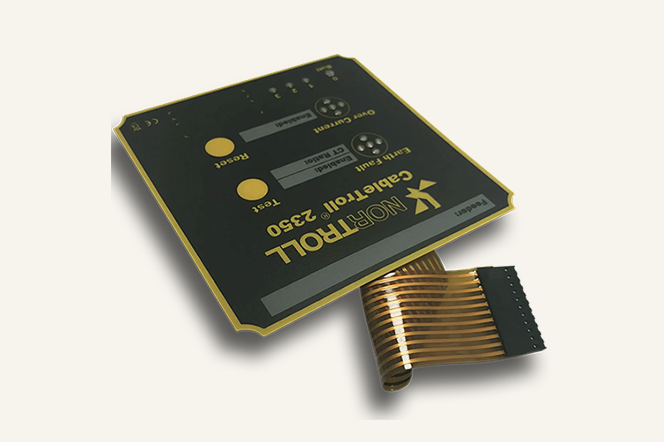
Flexible Membrane Switch
Bendable and lightweight, ideal for wearable and handheld devices, 100,000 bend cycles.
Want to know more about the deeper principles?
Hope you find the information useful!
Some Knowledge You May Need
What Is a Tactile Membrane Switch and How Does It Work?
Introduction: Why Tactile Membrane Switches Matter
In industrial control panels, medical devices, and consumer electronics, the reliability and responsiveness of the user interface is critical. Tactile membrane switches are a preferred solution thanks to their low profile, fast response time, and clear tactile feedback, making them a key human-machine interface component in many modern applications.
What Is a Tactile Membrane Switch?
A tactile membrane switch is a thin, flexible switch assembly that offers distinct physical feedback—often described as a “snap” or “click”—when pressed. It is composed of multiple layers, typically including:
Graphic overlay – the top layer that displays icons or user instructions
Spacer layer – separates the circuit layers to maintain an open circuit until activation
Circuit layer – conductive traces that carry the signal
Tactile dome – metal or polyester dome providing the click response
✅ Key feature: The tactile dome delivers a crisp tactile sensation, giving users physical confirmation that the switch has been activated.
How Does a Tactile Membrane Switch Work?
When a user presses the surface of the switch, pressure is applied to the tactile dome beneath the overlay. This dome collapses and makes contact with the lower circuit layer, completing the electrical circuit.
When the pressure is released, the dome returns to its original shape, and the circuit opens again. This snap-action mechanism enables fast, reliable signal input—ideal for applications where operator feedback and accuracy are essential.
Main Components Explained
Layer | Function |
---|---|
Graphic Overlay | Provides visual instructions and protects inner layers |
Tactile Dome | Produces physical feedback and triggers the circuit |
Spacer Layer | Maintains the open state of the circuit until pressed |
Circuit Layer | Conducts electricity when activated |
Rear Adhesive | Bonds the switch assembly to the application surface |
👉 Optional materials include stainless steel domes, PET circuits, silver or carbon conductive inks—all customizable based on application needs.
Where Are Tactile Membrane Switches Used?
Tactile membrane switches are used in systems where space-saving, low voltage operation, and reliable touch feedback are required. Typical applications include:
🏭 Industrial Automation – operator panels, CNC controllers
🏥 Medical Equipment – monitors, diagnostic devices
🔋 Consumer Electronics – remote controls, wearables
🚜 Transportation Systems – dashboards, heavy machinery controls
Key Benefits for Engineers and Buyers
✅ Positive tactile feedback for improved usability
✅ Ultra-slim design – ideal for space-constrained layouts
✅ Fully customizable shapes, colors, and icons
✅ Highly durable – rated for up to 1 million actuations
✅ Sealed and robust – IP65+ water/dust resistance available
Conclusion: Is a Tactile Membrane Switch Right for You?
If your project needs a low-profile switch interface that delivers clear tactile feedback, high reliability, and full customization, a tactile membrane switch is an excellent choice. Whether you’re an engineer selecting components or a buyer evaluating suppliers, knowing how this technology works will help you make an informed decision.
📩 Looking for a reliable manufacturer of tactile membrane switches? Contact us today to explore how we can develop a custom solution for your application.
Top 5 Advantages of Using Tactile Membrane Switches in Industrial Applications
Introduction: Why the Right Switch Matters in Industrial Design
In industrial environments, every component must be reliable, durable, and intuitive. The tactile membrane switch has become a popular choice in control panels, automation systems, and heavy machinery interfaces. But why do so many engineers and buyers choose tactile membrane switches over other interface technologies?
Here are the top 5 reasons these switches are ideal for industrial use.
1. Clear Tactile Feedback Improves User Accuracy
Operators often work in gloved or low-visibility environments, where visual confirmation of a button press isn’t enough. Tactile membrane switches provide a noticeable snap or click when pressed, giving immediate physical feedback.
✅ Benefit: Reduces mispresses, improves operational accuracy, and speeds up user response time.
2. Long Lifespan in Demanding Environments
Industrial settings are tough—there’s dust, moisture, vibration, and constant usage. High-quality tactile switches are built with sealed surfaces (IP65+), durable domes, and wear-resistant overlays, allowing them to withstand millions of cycles without failure.
✅ Benefit: Lower maintenance costs, fewer replacements, and uninterrupted performance in harsh conditions.
3. Compact and Customizable for Tight Spaces
Compared to traditional mechanical switches, membrane switches have an ultra-thin profile and can be easily customized in shape, layout, color, and iconography. This makes them ideal for space-constrained designs.
✅ Benefit: Flexible integration into control panels, handheld devices, and complex machinery with limited space.
4. Easy to Seal for Dust, Water, and Chemical Resistance
With no exposed moving parts, tactile membrane switches are easily sealed against liquids and debris. They can be designed to meet IP65, IP67, or even IP68 standards, making them perfect for outdoor or industrial use.
✅ Benefit: Enhanced reliability in wet, dusty, or corrosive environments, including food processing, medical, and agriculture industries.
5. Cost-Effective for High-Volume Production
Membrane switches are made using screen-printing and flexible circuit technology, which makes them highly economical for large production runs. Their long lifespan and reliability also reduce total cost of ownership over time.
✅ Benefit: Low per-unit cost, high return on investment, ideal for OEMs and equipment manufacturers.
Conclusion: An Industrial-Grade Interface You Can Trust
Tactile membrane switches offer a powerful combination of durability, user feedback, customizability, and cost-efficiency—making them a smart choice for industrial designers and procurement teams. Whether you’re building a next-gen control panel or upgrading legacy equipment, these switches deliver long-term value and operator confidence.
📩 Want to design a tactile membrane switch tailored for your industry? Contact our team for technical advice and a free quote.
How to Customize Tactile Membrane Switches for Harsh Environments (IP65+, UV, etc.)
Introduction: When the Environment Becomes the Challenge
In industries like outdoor automation, medical equipment, agriculture, or military systems, human-machine interfaces must perform under extreme conditions—moisture, dust, UV exposure, chemicals, or wide temperature swings.
This is where customized tactile membrane switches shine. With the right materials and design, these switches can be engineered to thrive in the harshest environments—without sacrificing reliability or performance.
1. Choose the Right IP Rating for Your Application
The Ingress Protection (IP) rating defines how well the switch resists dust and water.
IP Rating | Protection Level | Suitable For |
---|---|---|
IP65 | Dust-tight and protected against water jets | General outdoor and industrial use |
IP67 | Dust-tight and protected against immersion (up to 1m) | Medical, marine, or agriculture use |
IP68 | Dust-tight and protected against long-term immersion | Harsh environments, submerged use |
✅ Tip: For outdoor or washdown environments, aim for IP67+ designs with sealed perimeters and waterproof adhesives
2. Use UV-Resistant and Weatherproof Materials
Sunlight can degrade overlays, especially in outdoor applications. Using UV-stabilized polyester or polycarbonate overlays ensures long-lasting clarity, flexibility, and protection from yellowing, cracking, or fading.
✅ Recommended materials:
Autotex® polyester for high durability
Hard-coated polycarbonate for impact resistance
3. Optimize Dome and Circuit Design for Temperature Extremes
In extreme hot or cold conditions, the dome actuation force and electrical performance must remain stable.
✅ Design tips:
Use metal domes rated for -40°C to +85°C
Choose silver-based conductive inks for better temperature stability
Include venting channels to handle air pressure changes in sealed enclosures
4. Add Chemical and Abrasion Resistance Layers
In chemical plants or food processing facilities, membrane switches are often exposed to solvents, alcohol, disinfectants, or abrasion from frequent cleaning.
✅ Protective options:
Hard-coated overlay films
Clear polyester top films with chemical resistance
Embossed graphics sealed beneath the surface
5. Seal the Edges and Connectors Against Moisture
While the surface is often sealed, moisture can still penetrate via edges or tail connectors if not properly protected.
✅ Solutions include:
Perimeter gaskets (e.g., silicone)
Waterproof back adhesive (e.g., 3M 467MP + foam)
Heat-shrink tubing or epoxy potting at tail exit points
Conclusion: Customization Is Not Optional—It’s Critical
When standard switches won’t survive your working conditions, custom engineering becomes essential. By selecting the right materials, sealing methods, and component designs, your tactile membrane switch can be a long-term, high-performance solution—even in the harshest environments.
📩 Need a membrane switch for rugged use? Our engineering team can help you design one that meets your specific environmental challenges.
Actile vs. Non-Tactile Membrane Switches: Which Is Right for Your Application?
Introduction: Not All Membrane Switches Feel the Same
When designing a user interface for industrial, medical, or consumer devices, choosing between tactile and non-tactile membrane switches can significantly impact usability, durability, and cost.
So, how do you decide which one is the best fit for your application? This guide breaks down the differences and helps you choose the right switch for your specific needs.
1. What Is a Tactile Membrane Switch?
A tactile membrane switch includes a metal or polyester dome under the overlay, which gives a noticeable “click” feel when pressed. This tactile feedback confirms that the switch has been activated.
✅ Best for:
Industrial control panels
Medical equipment
Applications requiring user confirmation
2. What Is a Non-Tactile Membrane Switch?
A non-tactile membrane switch lacks the tactile dome. Instead, it uses flat circuit layers that make electrical contact when pressed. There is no snap or click, but these switches can still be very responsive.
✅ Best for:
High-speed keypad inputs
Environments requiring silent operation
Designs needing longer switch life
3. Side-by-Side Comparison Table
Feature | Tactile Switch | Non-Tactile Switch |
---|---|---|
User Feedback | Click/snap feel for confirmation | No tactile feedback |
Actuation Force | Higher (requires dome compression) | Lower (softer press) |
Typical Lifespan | 1–5 million actuations | Up to 10 million actuations |
Design Complexity | Requires dome layer | Simpler construction |
Use Case | Industrial, medical, outdoor equipment | Office equipment, touch panels, silent UI |
Cost (Generally) | Slightly higher due to dome component | More cost-efficient for high-volume input |
4. Which One Should You Choose?
👉 Choose Tactile If:
Your users need confirmation with every press
The interface will be used in gloved environments
You want to minimize input errors
👉 Choose Non-Tactile If:
You need fast, repetitive inputs
Your design requires a longer switch life
You want a silent, low-profile interface
5. Can You Combine Both? Hybrid Options Exist
Some designers opt for hybrid membrane switches—using tactile switches for key functions (e.g., start/stop) and non-tactile for numeric entry. This offers a balanced UX with performance and longevity.
Conclusion: It’s All About the Application
There is no one-size-fits-all answer. The decision between tactile and non-tactile membrane switches should be based on your end-user’s needs, environmental demands, and budget priorities.
📩 Need help choosing the right membrane switch for your design? Our team can evaluate your project specs and recommend the ideal interface solution.
Design Tips for Improving User Experience in Tactile Membrane Switch Interfaces
Introduction: UX Matters—Even in Industrial Interfaces
In modern equipment—from medical monitors to industrial control panels—user interface (UI) design plays a major role in overall product success. A tactile membrane switch isn’t just about functionality—it’s about how the operator feels, responds, and interacts with the device.
By integrating thoughtful design strategies, you can dramatically improve the efficiency, accuracy, and satisfaction of your users.
1. Optimize Tactile Feedback Based on User Environment
Not all applications require the same “click” feel. In industrial settings where gloves are worn, a stronger tactile response (e.g., metal dome, 300–500g force) is often preferred. In contrast, consumer devices may favor softer domes for a lighter touch.
✅ Tip:
Test different actuation forces (200g, 350g, 500g) with real users.
Match feedback level to your application: strong for outdoor/industrial, light for desktop or medical use.
2. Use Backlighting and Indicators for Visibility
Low-light or high-glare environments can make it difficult to locate or identify buttons. LED backlighting, fiber optic layers, or EL (electroluminescent) panels can improve visibility dramatically.
✅ Options to consider:
Selective backlighting only for key areas
Color-coded LEDs for function/status indication
Combine with translucent or windowed overlays
3. Prioritize Logical Layout and Finger Travel
Operators should be able to intuitively locate buttons without confusion or excessive movement. Use ergonomic spacing, logical grouping, and clear separation between functions.
✅ Design advice:
Place high-frequency keys closer to natural hand positions
Group similar functions together (e.g., start/stop, navigation keys)
Avoid placing critical buttons near “cancel” or “reset” keys
4. Customize Graphics for Clarity and Speed
Your graphic overlay is not just decoration—it’s the user’s primary communication channel with the machine. Use contrasting colors, clear icons, and legible fonts to eliminate guesswork.
✅ Best practices:
Use internationally recognized ISO icons where possible
Avoid small text sizes (recommend minimum 10pt)
Ensure good contrast between text and background (e.g., white on black)
5. Consider Surface Texture and Finish
The feel of the overlay affects both perception and usability. Matte finishes reduce glare, while gloss surfaces may highlight icons. Textured films can add grip and improve tactile targeting.
✅ Material tips:
Matte polyester for industrial panels
Textured hard-coated polycarbonate for medical or high-cleaning applications
Consider embossing for elevated key edges and tactile guidance
6. Minimize User Fatigue
In applications requiring frequent use (like control stations or diagnostic interfaces), user fatigue becomes a real issue. Optimize dome type, key spacing, and actuation force to reduce strain over time.
✅ Ergonomic tips:
Use low-profile domes for soft touch
Allow finger rest zones if space permits
Avoid overly stiff keys in high-usage applications
Conclusion: Great UX Is Built Into the Details
A well-designed tactile membrane switch does more than send a signal—it creates a seamless, comfortable, and intuitive interaction between user and machine. With the right attention to feedback, layout, visibility, and material selection, you can elevate your product’s perceived quality and ensure operators stay efficient and satisfied.
📩 Need help optimizing your membrane switch interface? Our engineers can support you with design guidance, prototypes, and full customization.
Quality and Testing Standards for Tactile Membrane Switches: What Buyers Should Know
Introduction: Not All Switches Are Created Equal
For procurement managers and engineers, selecting a tactile membrane switch isn’t just about the initial specs—it’s about long-term performance, reliability, and compliance.
Understanding the industry standards, testing procedures, and quality indicators is essential to ensure that your switch will perform as expected in the field. Here’s what every buyer should know.
1. Key Performance Metrics to Check
When evaluating membrane switch quality, the following parameters are critical:
Parameter | Why It Matters | Typical Standard |
---|---|---|
Actuation Force | Ensures consistent user experience | 150g–500g based on application |
Tactile Feedback | User confirmation and responsiveness | Dome rebound consistency >90% |
Lifespan (Cycles) | Reliability over time | 1–5 million actuations |
Contact Resistance | Electrical signal integrity | <100 ohms (typical) |
Operating Temp. | Suitability for harsh environments | -40°C to +85°C |
✅ Tip: Always request a test report from your supplier to verify actual performance.
2. Essential Testing Procedures You Should Expect
Reliable suppliers will perform comprehensive testing across the following areas:
a. Life Cycle Testing
Simulates repetitive use to ensure the switch maintains function over millions of presses.
b. High/Low Temperature Testing
Verifies stable performance under thermal stress (typically -40°C to +85°C).
c. Humidity and Salt Spray Testing
Tests for corrosion and oxidation in humid or marine environments.
d. UV Aging Test
Assesses the overlay’s resistance to discoloration or brittleness under UV light.
e. Electrical Resistance Testing
Checks conductivity paths to detect broken traces or unstable contact points.
f. Waterproof/Dustproof Testing (IP65–IP68)
Ensures sealing effectiveness—especially for outdoor or industrial use.
3. Certification and Compliance Standards
Buyers should always ask whether the membrane switch complies with relevant international certifications:
ISO 9001 – Quality management system compliance
RoHS/REACH – Restriction of hazardous substances in materials
UL 94 – Flame rating for materials used in overlays
IPC-2221/2222 – Design and layout standards for printed circuit boards
✅ Pro Tip: If your application is medical, aerospace, or military-related, insist on documentation for traceability and material declarations.
4. Common Quality Failures and How to Prevent Them
Understanding what can go wrong helps you make smarter buying decisions:
Common Issue | Root Cause | Prevention Strategy |
---|---|---|
Dome collapse or fatigue | Poor material or overuse | Use high-grade domes, limit actuation force |
Overlay peeling | Incompatible adhesive or poor sealing | Match adhesive to surface material |
Signal dropout/interference | Bad silver ink trace or contamination | Require IPC-quality conductive inks |
Color fading or cracking | Low-quality overlays | Use UV-resistant, hard-coated films |
5. Questions to Ask Your Supplier Before Ordering
Can you provide full testing reports (e.g., life cycle, temperature, IP rating)?
What certifications do your materials and production lines meet?
Do you perform 100% electrical testing before shipment?
How do you handle quality issues or returns?
Can I receive pre-production samples for qualification?
Conclusion: Quality Isn’t Optional—It’s a Competitive Advantage
High-quality tactile membrane switches minimize field failures, reduce maintenance costs, and increase user satisfaction. By understanding the standards and asking the right questions, you can confidently choose a supplier who delivers not just components—but long-term reliability.
📩 Need a supplier with full testing and certifications? Contact us for test data, sample evaluation, and a customized proposal.