High-Quality Membrane Switches Just in One Place - The Ultimate Solutions
Your One-Stop Solution for Industrial and Consumer Applications
Hi, I’m Lily from SwitchNova. Let me introduce our membrane switch solutions.
We have over 10 years of experience in providing high-quality membrane switches to global industry leaders. Explore our reliable and customizable solutions designed for industrial automation, medical devices, and consumer electronics.
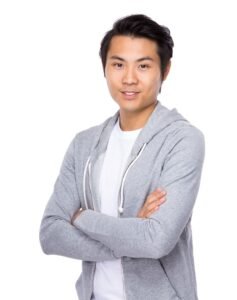
Why Choose SwitchNova ’s Switches
Reliable, high-quality switches designed for demanding applications and long-term performance.
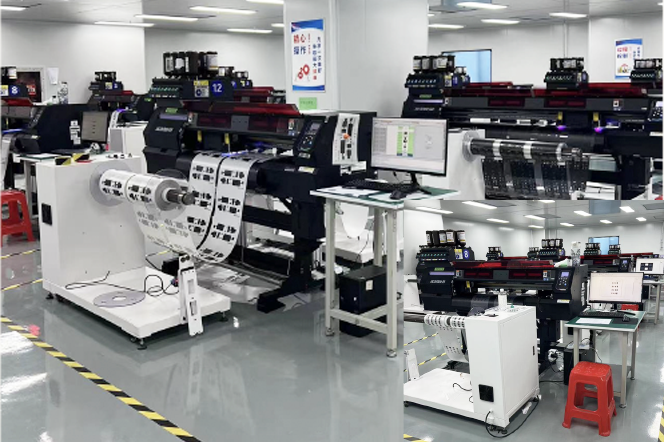
Advanced Manufacturing
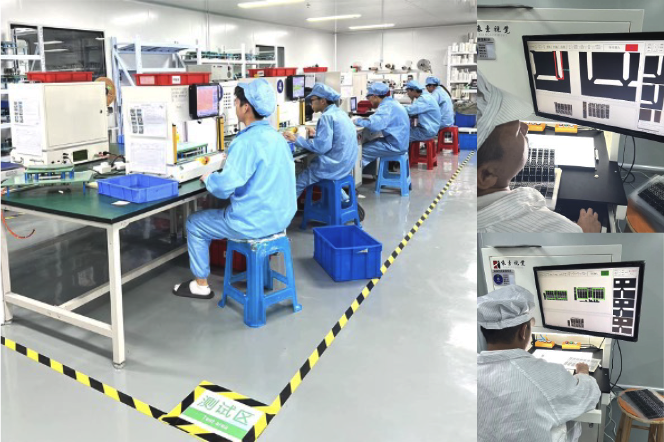
Strict Quality Control
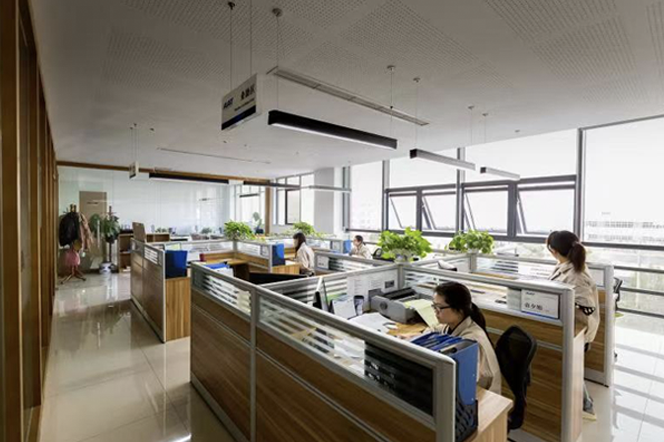
Fast and Efficient Response
Trusted by Global Brands
We proudly serve industry leaders with reliable, high-performance membrane switch solutions.
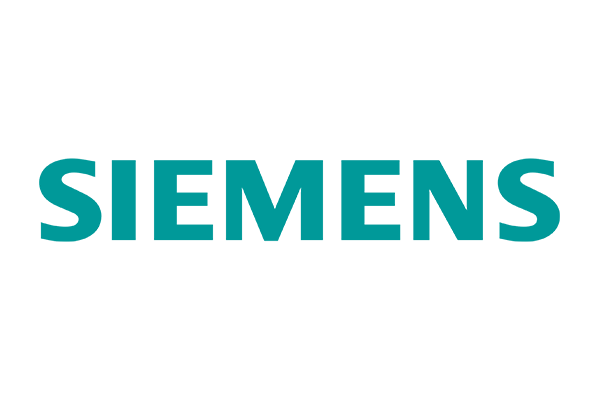
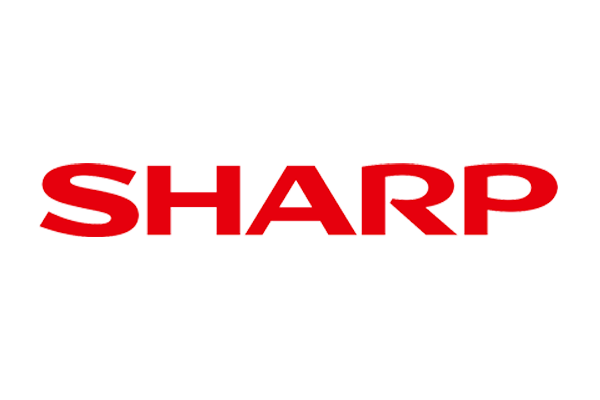
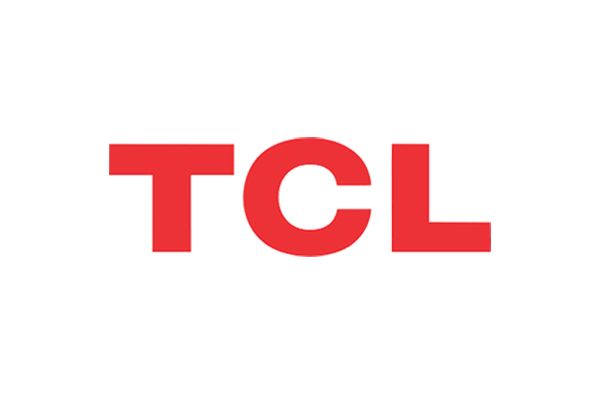
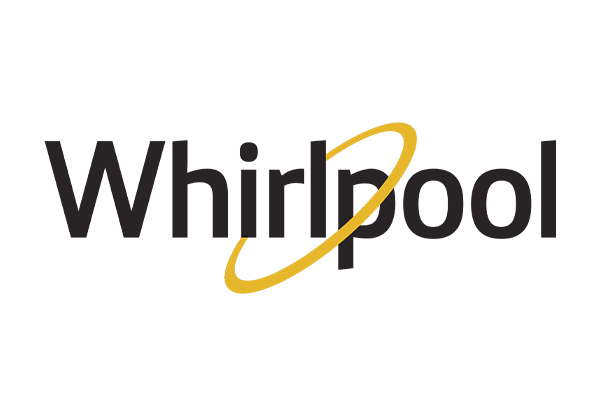
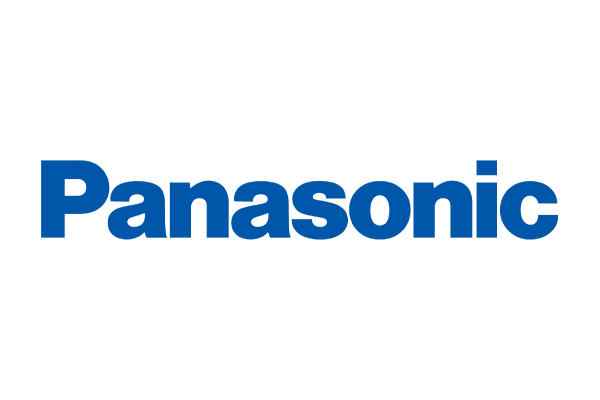
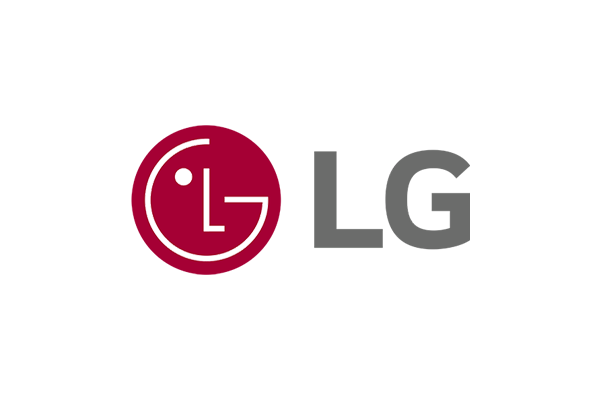
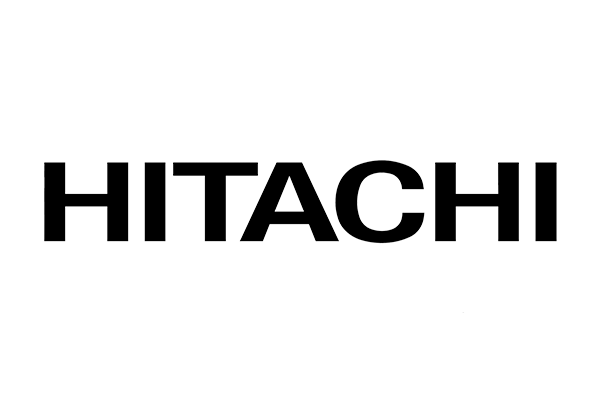
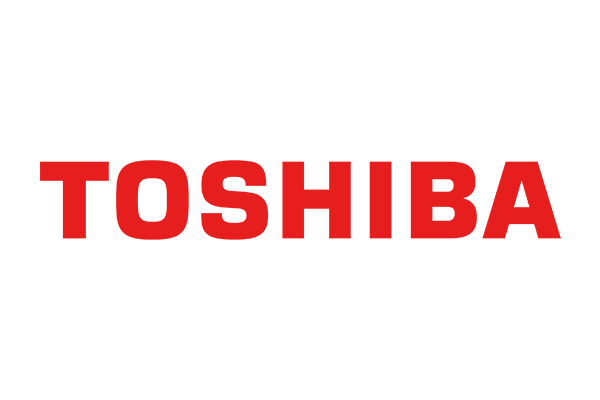
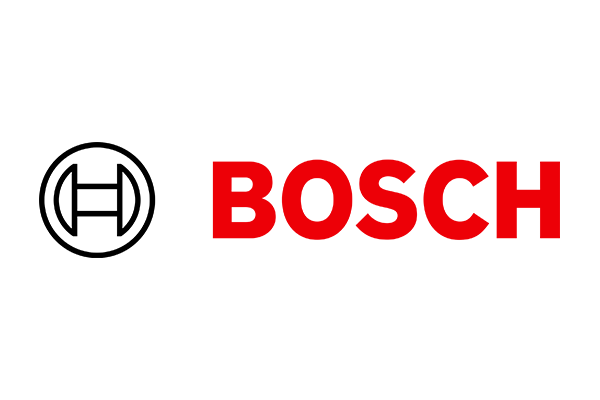
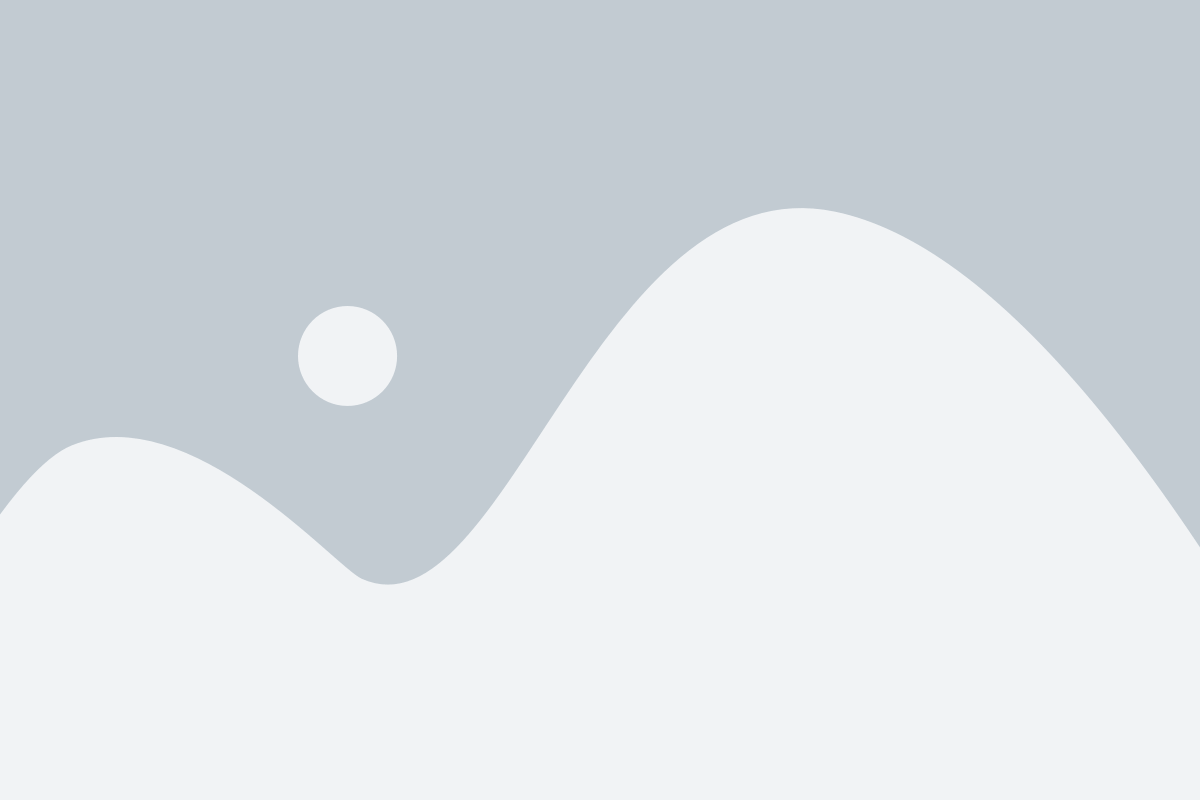
Our Best-Selling Switches
Discover our best-selling membrane switches designed for various industries.
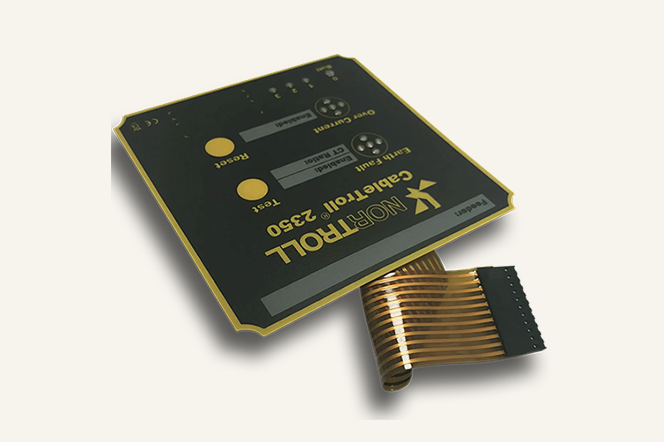
Tactile Membrane Switch
High tactile feedback, durable design for industrial and medical applications, IP65 rated.
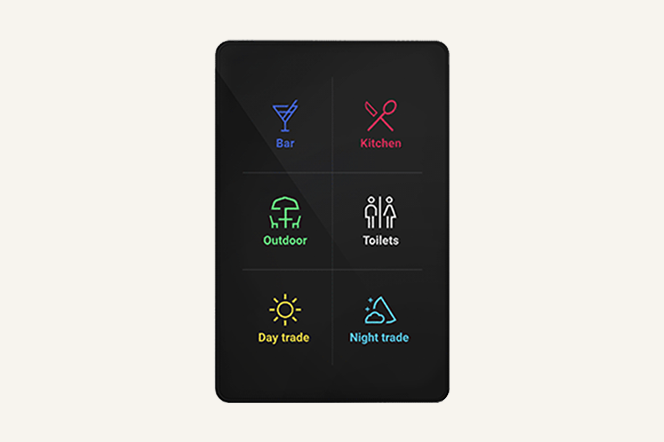
Capacitive Membrane Switch
Responsive touch control, anti-interference design for electronics and automotive, 10ms response.
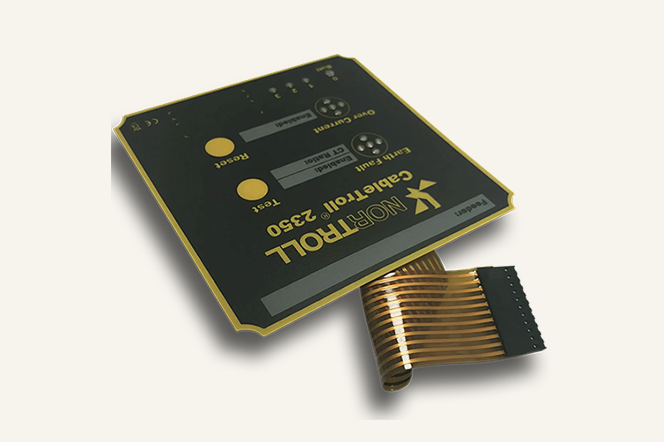
Flexible Membrane Switch
Bendable and lightweight, ideal for wearable and handheld devices, 100,000 bend cycles.
Want to know more about the deeper principles?
Hope you find the information useful!
Some Knowledge You May Need
Comprehensive Guide to Membrane Switches: Everything Engineers and Purchasers Need to Know
Construction of a Membrane Switch
A membrane switch typically consists of five or more layers that are printed on a flexible substrate, each serving a specific purpose. Let’s break down the common layers found in a membrane switch:
A membrane switch is a versatile, user-friendly interface used to control electronic devices. It is a custom switch assembly that consists of multiple layers, designed to open or close electrical contacts upon activation. Unlike traditional mechanical switches, membrane switches are made of flexible substrates, offering a sleek, low-profile design and the ability to integrate easily into various devices. Whether you’re in charge of procurement or involved in product development, understanding the design, materials, applications, and benefits of membrane switches is crucial for making informed decisions.
What is a Membrane Switch?
A membrane switch is a thin, flexible user interface that allows interaction between humans and machines by completing an electrical circuit when pressed. Membrane switches are commonly used in consumer electronics, industrial applications, and medical devices, providing a clean, durable, and efficient way to operate machinery or appliances.
Key Features of Membrane Switches:
- Durability: Fewer mechanical parts mean membrane switches are resistant to wear and tear.
- Customizability: Can be tailored with unique graphics, colors, and tactile feedback options.
- Compact Design: Their slim profile allows them to fit into space-constrained environments.
- Cost-Effective: More affordable than mechanical switches, especially for high-volume production.
Layer | Purpose |
---|---|
Graphic Overlay | This top layer provides the graphic design and user interface, including buttons and symbols. |
Spacer Top Sheet | This layer separates the graphic overlay from the conductive layer, allowing for the switch to be pressed without direct contact. |
Conductive Layer | Made from conductive materials like carbon or silver, this layer forms the circuit when pressed. |
Spacer Bottom Sheet | The bottom layer separates the conductive layer from the adhesive layer, ensuring no accidental contact. |
Mounting Adhesive | The final layer used to attach the membrane switch to the surface of the device, ensuring stability and ease of installation. |
Construction Process:
- Pressure-Sensitive Adhesive: Membrane switches are typically assembled using pressure-sensitive adhesives, which means they are flexible and easy to apply.
- Printed Circuits: The circuit layers are usually printed on flexible substrates like Polyester (PET) or Polycarbonate to ensure flexibility and durability.
Backlighting for Membrane Switches
Membrane switches can be equipped with backlighting to enhance visibility, especially in low-light environments. There are three common methods used for backlighting:
Backlighting Method | Description |
---|---|
LED Lights | LEDs emit light from beneath the surface, ideal for illuminating the switch’s surface. |
Optical Fiber | Woven fiber-optic cloth is used to transmit light through the membrane, providing uniform lighting. |
Electroluminescent (EL) Film | EL film emits light when an electric current is applied, providing a smooth, even glow. |
These backlighting options make membrane switches an excellent choice for applications such as medical devices, industrial equipment, and consumer electronics, where visibility and user interaction are key.
Applications of Membrane Switches
Membrane switches are used in a wide range of industries and applications due to their flexibility, durability, and ease of use. Below are some of the key areas where membrane switches are commonly employed:
Industry/Application | Typical Use Cases |
---|---|
Consumer Electronics | Used in devices such as microwaves, coffee machines, and remote controls. |
Medical Devices | Common in diagnostic machines, patient monitoring equipment, and portable medical devices. |
Industrial Control Systems | Used in machinery and automation systems for control panels. |
Automotive | Found in vehicle dashboards, entertainment systems, and climate control. |
Membrane switches are ideal for human-machine interfaces, providing a reliable and efficient way for users to interact with electronic devices across various fields.
Benefits of Membrane Switches
- Cost-Effective Manufacturing: Membrane switches are generally more affordable than mechanical switches, especially when produced in large volumes.
- Long Lifespan: Due to fewer moving parts, membrane switches are highly durable and can last longer than traditional mechanical switches.
- Enhanced Functionality: With features such as tactile feedback, backlighting, and custom graphics, membrane switches provide both functional and aesthetic benefits.
- Resistance to Environmental Factors: Many membrane switches are designed to withstand moisture, dust, and UV exposure, making them suitable for use in demanding environments.
Design Considerations for Membrane Switches
When designing a membrane switch, several factors need to be taken into account to ensure optimal performance and longevity. Here are some important considerations:
Design Consideration | Key Points |
---|---|
Material Selection | Choose materials that provide the required durability (e.g., UV-resistant, scratch-resistant). |
Button Embossing | Embossing buttons for tactile feedback can improve user experience. |
Color & Graphics | Ensure clear, visible graphics for easy user interaction. |
Backlight Integration | Choose the appropriate backlighting option for enhanced visibility. |
Tactile Feedback | Consider adding a metal dome or other tactile components to improve the user experience. |
Quality Control and Testing
To ensure the highest quality and reliability, membrane switches undergo extensive testing during the production process:
Testing Area | Key Tests |
---|---|
Circuit Functionality | Check for proper electrical connections and absence of shorts. |
Tactile Feedback | Verify that the button embossing provides the correct tactile feel. |
Backlighting Consistency | Ensure even lighting across the switch for readability. |
Durability Testing | Assess the switch’s performance under conditions like moisture, temperature, and heavy use. |
Why Choose SwitchNova for Membrane Switches?
At SwitchNova, we pride ourselves on delivering high-quality membrane switches that meet the unique needs of our clients. Here’s why our customers trust us:
- Custom Solutions: We offer fully customizable membrane switches to match your specific requirements.
- Reliable Performance: Our switches are designed to perform consistently under a variety of environmental conditions.
- Competitive Pricing: We provide cost-effective solutions without compromising on quality.
- Expert Support: From design to production, our experienced team is here to guide you through every step of the process.
If you’re looking for a high-quality, reliable, and cost-effective membrane switch solution, SwitchNova is your go-to partner. Contact us today to learn more about how we can help you with your project.
Conclusion
Membrane switches are an essential component in modern electronics, offering an innovative, durable, and cost-effective interface solution for a variety of applications. At SwitchNova, we specialize in designing and manufacturing custom membrane switches that enhance the user experience, improve functionality, and ensure long-lasting performance. Whether you’re developing a new consumer product or upgrading an industrial system, we provide the expertise and technology to deliver the best solution for your needs.
What Is a Membrane Switch and How Does It Work?
In today’s fast-paced industrial and medical environments, reliability and efficiency are non-negotiable. One often-overlooked component that plays a vital role in user interface design is the membrane switch. But what exactly is a membrane switch, and how does it work? If you’re an engineer, product designer, or sourcing professional, this guide will give you a clear and practical understanding.
What Is a Membrane Switch?
A membrane switch is a low-profile, user-interface component that allows users to communicate with electronic devices. It’s commonly used in control panels, medical equipment, industrial machinery, and consumer electronics due to its durability, compact design, and customization options.
Rather than using traditional mechanical parts, a membrane switch relies on pressure-based electrical contact. This makes it a sealed, flexible, and highly reliable solution for environments where moisture, dust, or chemicals are present.
Key Components of a Membrane Switch
A typical membrane switch is made up of multiple functional layers. The following table provides a clear overview:
Layer | Function | Material | Notes |
---|---|---|---|
Graphic Overlay | User interface display | PET / Polycarbonate | UV and chemical resistant |
Spacer Layer | Prevents shorting between circuits | Adhesive PET | Defines button travel distance |
Top Circuit Layer | Part of the switching circuit | Silver ink on PET | Activates when pressed |
Bottom Circuit Layer | Completes the circuit | Silver or carbon ink | Forms contact with top layer |
Dome Layer (opt.) | Provides tactile feel | Metal dome | Adds "click" feedback for better UX |
Back Adhesive (opt.) | Mounting to enclosure | 3M adhesive / custom material | Depends on final installation requirement |
How Does It Work?
The operation is simple yet effective:
User presses a button on the graphic overlay.
The pressure causes the top circuit layer to flex downward.
This flexing connects the top and bottom circuit layers.
An electrical signal is sent to the device’s control system.
When pressure is released, the layers return to their original position.
Because there are no moving mechanical parts, the system is extremely reliable and capable of millions of actuations.
Advantages of Membrane Switches
✅ Compact and Lightweight – Ideal for portable or space-constrained devices.
✅ Sealed and Durable – Resistant to water, dust, and chemicals.
✅ Customizable Design – Tailor graphics, colors, shapes, and LED backlighting.
✅ Cost-Effective – Especially in medium-to-high volume production.
✅ Easy to Integrate – Compatible with capacitive touch, FPCs, or PCBs.
Common Applications
Medical Equipment: Diagnostic machines, handheld monitors, infusion pumps
Industrial Control Panels: CNC machinery, factory automation, safety systems
Consumer Electronics: Remote controls, appliances, fitness equipment
Military & Aerospace: Ruggedized devices requiring long lifecycle and sealing
Final Thoughts
A membrane switch may seem like a simple component, but it plays a critical role in product usability, reliability, and branding. When properly designed, it ensures seamless interaction between user and machine — whether in a hospital, a factory, or a harsh outdoor environment.
If you’re developing a product that requires a user interface that is durable, cost-effective, and fully customizable, a membrane switch is a smart choice.
Construction of ****
A membrane switch *****
Layer | Purpose |
---|---|
Graphic Overlay | This top layer provides the graphic design and user interface, including buttons and symbols. |
Spacer Top Sheet | This layer separates the graphic overlay from the conductive layer, allowing for the switch to be pressed without direct contact. |
Conductive Layer | Made from conductive materials like carbon or silver, this layer forms the circuit when pressed. |
Spacer Bottom Sheet | The bottom layer separates the conductive layer from the adhesive layer, ensuring no accidental contact. |
Mounting Adhesive | The final layer used to attach the membrane switch to the surface of the device, ensuring stability and ease of installation. |
Top 5 Benefits of Using Membrane Switches in Industrial Applications
In the industrial world, every component matters — especially those that operators interact with every single day. A membrane switch may be small, but in demanding industrial environments, it plays a critical role in ensuring equipment reliability, user efficiency, and overall operational safety.
Here are the top five reasons why membrane switches are a smart choice for engineers and procurement professionals looking for high-performance, cost-effective human-machine interface (HMI) solutions.
1. Exceptional Durability in Harsh Environments
Industrial environments are rarely gentle — exposure to dust, moisture, oil, vibration, chemicals, and temperature extremes is common. Membrane switches are designed to handle all of that.
Sealed construction (IP65–IP67 capable) protects internal circuitry
Materials like PET and polycarbonate resist abrasion and chemical exposure
No moving mechanical parts = fewer failure points
👉 Ideal for CNC machines, factory floors, and outdoor installations.
2. Customizable Design for Every Application
Unlike off-the-shelf mechanical buttons, membrane switches are fully customizable — from graphic overlays to tactile response, from backlighting to circuit layout.
Customizable Feature | Options Available |
---|---|
Graphic Overlay | Colors, logos, icons, texture |
Tactile Feedback | Flat or tactile domes (metal or polydome) |
Backlighting | LED, fiber optic, electroluminescent (EL) |
Circuit Design | Flexible circuits (PET), rigid PCB, or hybrid |
Connectors | Male/female headers, ZIF, FPC tail |
🛠️ This flexibility allows engineers to design intuitive, ergonomic, and brand-consistent interfaces for any machine.
3. Low Profile and Lightweight Construction
Membrane switches are thin (typically 0.5–1.5 mm) and lightweight, making them perfect for applications where space and weight are limited — such as portable devices, handheld tools, and embedded control panels.
Reduces device bulk
Easy integration onto curved or compact surfaces
No bulky hardware or soldering required
📦 Smaller footprint = more room for innovation.
4. Cost Efficiency for Mid-to-High Volume Production
For OEMs and device manufacturers, cost control is essential. Membrane switches provide a low-cost HMI solution without sacrificing quality — especially when produced in medium or high quantities.
Economical materials and scalable screen printing process
Lower tooling and setup cost compared to mechanical keypads
Long operational lifespan = fewer replacements, lower maintenance cost
💰 Procurement managers love the balance of performance and affordability.
5. Improved Reliability and User Experience
Membrane switches can endure millions of actuations, ensuring consistent performance over time. Tactile domes and feedback mechanisms also enhance the operator’s touch accuracy and response time, reducing input errors.
Precise control with tactile feedback
No bouncing or double-click errors
Can integrate with LEDs, sensors, and EMI shielding for added functionality
🧠 Reliable input = better system control = fewer downtimes.
Final Thoughts
In the world of industrial automation, membrane switches offer a rare combination of rugged performance, tailored design, and cost-efficiency. Whether you’re designing a control panel for a food processing machine or a user interface for a heavy-duty diagnostics device, membrane switches deliver where it matters most.
Looking to integrate membrane switches into your next project? Our team at Suzhou Taurus Materials Technology specializes in custom HMI solutions tailored to industrial demands. Contact us for engineering support or a free consultation.
How to Design a Custom Membrane Switch: A Step-by-Step Guide for Engineers
Designing a custom membrane switch is not just about picking buttons and layouts—it’s about optimizing functionality, durability, and user experience. Whether you’re building a medical device, an industrial controller, or a rugged handheld, a well-designed membrane switch can make your product stand out.
This guide will walk you through the 7 essential steps of designing a membrane switch that meets your project’s technical and functional requirements.
Step 1: Define the Application Requirements
Before diving into materials or graphics, clarify the operating conditions and usage expectations:
Environment: Will it be exposed to moisture, chemicals, UV light, or dust?
Usage frequency: How many actuations per day/month/year?
User interface type: Tactile (with domes) or non-tactile (flat)?
Mounting method: Panel mount, handheld, or integrated into a larger assembly?
🎯 Clear technical goals help engineers choose the right materials and construction.
Step 2: Choose the Right Graphic Overlay Material
The graphic overlay is the user-facing layer. Choosing the correct material impacts both aesthetics and durability:
Material | Features | Best For |
---|---|---|
Polyester (PET) | Excellent chemical and abrasion resistance | Industrial & medical devices |
Polycarbonate (PC) | Easy to print, cost-effective | Consumer products, indoor use |
Add UV coatings, anti-glare, or anti-microbial finishes based on the use case.
Decide on embossing (raised buttons) for tactile definition.
Step 3: Design the Circuit Layout
The switch circuit can be printed on flexible PET or integrated with a rigid PCB:
Contact design: Silver ink (conductive), carbon for resistance
Trace routing: Compact layout with minimal crossover
Connector type: ZIF tail, female header, or custom FPC
⚙️ Ensure proper layer alignment and spacing for reliable actuation.
Step 4: Select Dome Type and Feedback Level
Depending on user preference and application, you may choose:
Metal domes: Provide crisp, tactile “click” (70g–300g force)
Polydomes: Softer tactile feedback, cost-effective
Flat switches: For environments where silent operation or waterproofing is critical
🧠 The feel of the button greatly influences perceived product quality.
Step 5: Determine Backlighting or Display Integration
If visibility in low light is important, consider integrating:
LEDs: Ideal for individual key illumination
EL backlighting: Uniform glow, thin profile
Fiber optics: Light distribution across multiple buttons
Add windows for LCDs or indicators
💡 Backlighting enhances usability, especially in medical and industrial settings.
Step 6: Plan for Mounting and Adhesive Layers
The final switch needs to be securely mounted to your product:
Choose 3M adhesive based on surface type (plastic, metal, textured, etc.)
Consider venting, shielding, or gasket sealing if required
Ensure tail exit orientation fits your device’s internal layout
📐 A great design is also easy to assemble and install.
Step 7: Prototyping and Testing
Once the design is complete:
Request a functional prototype for testing
Validate electrical performance, tactile feel, and fit
Adjust design based on feedback
Finalize for mass production with approved drawing & BOM
✅ Early validation saves time and prevents costly revisions.
Final Thoughts
A membrane switch isn’t just a layer of buttons—it’s a carefully engineered interface that connects your users to your technology. By following these steps, engineers can ensure that the switch will deliver on reliability, performance, and user satisfaction.
Need support with your next custom design? Our team at SwichNova specializes in full-solution membrane switch engineering, from design consulting to production.
📩 Contact us today for free design guidance or a sample quote.
Membrane Switch vs. Mechanical Switch: Which Is Better for Your Application?
When designing a control interface for industrial, medical, or consumer products, one of the most important decisions is:Should you use a membrane switch or a mechanical switch?
Both technologies have their advantages—and the right choice depends on your environmental conditions, user requirements, product lifecycle, and budget. In this article, we’ll break down the key differences, so you can decide which one suits your application best.
What Is a Membrane Switch?
A membrane switch is a flat, flexible user interface that uses pressure-activated electrical contact between layers of conductive material. It is often integrated into sealed panels, and widely used in industrial, medical, and outdoor equipment.
What Is a Mechanical Switch?
A mechanical switch involves a physical moving part (like a spring or lever) to open or close a circuit. Common in keyboards, machinery panels, and devices that require distinct tactile feel, it provides strong mechanical feedback and often higher current capacity.
Key Differences at a Glance
Here’s a side-by-side comparison to help you evaluate:
Feature / Factor | Membrane Switch | Mechanical Switch |
---|---|---|
Design Profile | Ultra-thin, flat | Bulkier, requires more space |
Tactile Feedback | Optional (metal dome, polydome, or flat) | Strong mechanical click |
Durability (Lifespan) | 1–5 million actuations | 100K–10 million actuations |
Sealing (IP Rating) | Easily sealed up to IP67 | Difficult to fully seal |
Environmental Resistance | Excellent (moisture, dust, chemicals) | Poor without external sealing |
Customization | Highly customizable graphics and layout | Limited design flexibility |
Backlighting & Graphics | Easy to integrate LED/EL lighting | Not easy to integrate |
Maintenance | Low maintenance, sealed surface | Higher wear and tear over time |
Cost (per unit) | Lower (especially for high volume) | Higher due to mechanical parts |
Typical Applications | Medical, industrial, outdoor controls | Keyboards, control knobs, tactile panels |
When to Choose a Membrane Switch
✅ You need a sealed, reliable interface for harsh environments
✅ Your product requires custom branding or an integrated display
✅ Space-saving and lightweight design is a priority
✅ You want lower long-term costs for high-volume production
✅ The user interface does not require heavy tactile force
👉 Common in medical devices, handheld tools, factory automation panels, outdoor terminals
When to Choose a Mechanical Switch
✅ Tactile feedback is essential to your application
✅ You’re working on low-volume products or prototypes
✅ Your circuit needs to handle higher voltages or currents
✅ The design allows space for bulkier components
✅ You expect frequent replacement or servicing
👉 Common in mechanical keyboards, industrial control knobs, heavy-duty equipment
Final Thoughts
There’s no one-size-fits-all solution. Choosing between a membrane switch and a mechanical switch depends entirely on the end-user expectations, environmental requirements, and design constraints of your project.
If you’re unsure which direction to go, our engineering team at SwichNova is happy to help. We provide expert consultation, sample design support, and high-quality custom membrane switch production tailored to your specific needs.
📩 Talk to us today for a personalized recommendation or free design review.
How to Ensure Reliability and Durability in Harsh Environments
In industrial, medical, and outdoor applications, membrane switches must perform reliably—even under extreme conditions like moisture, chemicals, UV exposure, temperature swings, or mechanical stress. A failure could lead to costly downtime, safety issues, or product recalls.
So how do you design a membrane switch that can withstand harsh environments and still operate flawlessly for years?
Here are the 5 key strategies engineers and sourcing managers should follow to ensure maximum reliability and durability.
1. Choose the Right Overlay Material for the Environment
The graphic overlay is your first line of defense against environmental stress.
Material | Key Features | Best Use Cases |
---|---|---|
Polyester (PET) | High abrasion, chemical, and UV resistance | Industrial equipment, medical devices |
Polycarbonate (PC) | Good clarity and formability, less durable | Indoor controls, short lifecycle devices |
📌 PET is highly recommended for applications involving solvents, repeated cleaning, or outdoor exposure.
Enhance durability by adding:
Hard coatings (scratch resistance)
UV inhibitors (outdoor use)
Antimicrobial films (medical settings)
2. Use Sealed Construction with High IP Ratings
A well-sealed membrane switch prevents moisture, dust, and contaminants from entering critical areas.
Target IP65–IP67 ratings for outdoor or washdown environments
Use laser-cut adhesive spacers to maintain sealing integrity
Design with vent channels if pressure equalization is needed
💡 SwichNova specializes in fully-sealed, multi-layer designs for high-humidity and corrosive environments.
3. Select Chemically-Resistant Inks and Adhesives
Standard inks and adhesives can degrade when exposed to industrial chemicals or temperature extremes.
✅ Use silver or carbon conductive inks rated for chemical resistance
✅ Choose 3M industrial adhesives based on surface energy, temperature, and chemical exposure
✅ Verify ink/substrate compatibility through chemical soak testing
🧪 We recommend accelerated aging tests to simulate 3–5 years of field exposure.
4. Reinforce Circuit Layers and Button Areas
Prolong mechanical lifespan by reinforcing the most-used areas:
Add metal domes or polydomes for tactile feedback
Include EMI shielding for electronic interference protection
Use double-layer circuits or PCB hybrid designs for extra stiffness
Reinforce tail exit areas to prevent cable breakage from repeated flexing
🔧 Critical for devices with constant button pressing or exposed to vibration.
5. Conduct Rigorous Testing Before Mass Production
To guarantee long-term reliability:
Perform environmental tests (humidity, salt spray, thermal cycling)
Run life cycle tests (1M+ actuations) under load
Test in real-world conditions, not just lab simulations
Collaborate with your membrane switch supplier for custom testing protocols
📊 At SwichNova, we offer full reliability testing reports for industrial and medical clients.
Final Thoughts
Designing for harsh environments is about more than just using strong materials—it’s about engineering at every layer, from adhesive to overlay, to ensure years of worry-free performance.
Whether you’re developing for factory automation, outdoor controls, or medical diagnostics, SwichNova helps you build membrane switches that last—even in the most demanding conditions.
📩 Need help validating your design for extreme environments? Contact our engineering team today for expert advice and sample evaluation.
What Certifications and Testing Standards Should a Quality Membrane Switch Meet?
When sourcing membrane switches for medical devices, industrial controls, or consumer electronics, ensuring product reliability is just one part of the equation. For many applications—especially in North America and Europe—your membrane switch must also meet specific international certifications and testing standards.
These standards are not just “nice to have” — they are often mandatory for compliance, safety, and market entry.
In this article, we’ll walk you through the key certifications and testing protocols that a quality membrane switch should meet.
1. RoHS Compliance (Restriction of Hazardous Substances)
Region: European Union (and widely adopted globally)
Why it matters: Ensures the membrane switch is free from hazardous substances like lead, mercury, cadmium, hexavalent chromium, etc.
SwichNova Guarantee: All materials used in our membrane switches are 100% RoHS compliant, including inks, adhesives, and overlays.
✅ Critical for all electronic products sold in the EU and many parts of North America.
2. REACH Regulation (Registration, Evaluation, Authorization and Restriction of Chemicals)
Region: European Union
Why it matters: Covers SVHCs (Substances of Very High Concern) that may cause health or environmental risks.
Best Practice: Request REACH declarations from your supplier for long-term sustainability compliance.
🧪 Especially important for medical and wearables markets.
3. UL Certification (Underwriters Laboratories)
Region: Primarily North America
Why it matters: UL certifies the flame resistance, electrical insulation, and safety of components used in electronic assemblies.
Applicable Tests:
UL 94 (Flammability rating – e.g., V-0, V-2)
UL 969 (Marking and labeling systems)
🛡️ If your product requires UL certification, your membrane switch must use UL-recognized materials.
4. IP Rating (Ingress Protection)
Region: Global
Why it matters: Specifies how well the membrane switch is sealed against dust and water ingress.
Common Ratings:
IP65 – Dust-tight and protected from water jets
IP67 – Submersible for short periods
Testing Includes:
High-pressure water spray
Dust chamber exposure
Submersion validation
🌧️ Critical for outdoor, industrial, food processing, and medical washdown equipment.
5. Environmental & Mechanical Testing
A quality membrane switch should pass rigorous in-house or third-party validation tests:
Test Type | Purpose |
---|---|
Temperature Cycling | Tests expansion/contraction resistance |
Humidity Exposure | Evaluates adhesion and circuit integrity |
UV Aging | Simulates long-term outdoor exposure |
Life Cycle Testing | Validates actuation durability (1M+ cycles) |
Chemical Resistance | Confirms overlay/ink/adhesive durability |
Flex Testing | Ensures cable tail doesn’t crack or peel |
🧪 At SwichNova, every production batch can include these tests based on your application needs.
6. ISO 9001:2015 Quality Management System
Why it matters: This standard ensures consistent production quality, traceability, and continuous improvement in manufacturing.
SwichNova Status: Our facility operates under ISO 9001:2015 with full traceability from raw material to shipment.
📋 An essential signal of quality assurance for global OEM clients.
Final Thoughts
Certifications and testing standards are not just checkboxes—they are essential for:
Ensuring safety, consistency, and market compliance
Reducing product liability risks
Building trust with your end-users
At SwichNova, we help you meet these standards from the design stage through production, offering test reports, compliance documents, and full traceability upon request.
📩 Need to ensure your membrane switch meets international certification standards? Contact us for technical guidance, compliance documentation, or custom testing support.
Title
文章段落
Test Type | Purpose |
---|---|
Temperature Cycling | Tests expansion/contraction resistance |
Humidity Exposure | Evaluates adhesion and circuit integrity |
UV Aging | Simulates long-term outdoor exposure |
Life Cycle Testing | Validates actuation durability (1M+ cycles) |
Chemical Resistance | Confirms overlay/ink/adhesive durability |
Flex Testing | Ensures cable tail doesn’t crack or peel |